Neue nicht-konventionelle Methoden zur Mikro- und Nanostrukturierung von Polymeroberflächen
Forschungsbericht (importiert) 2006 - Max-Planck-Institut für Polymerforschung
1. Einleitung
Auf der Suche nach neuen Methoden, um Oberflächen im Mikro- und Nanometerbereich zu strukturieren, bedient man sich nicht nur konventioneller Methoden wie man sie aus der Silizium- und Halbleiterindustrie kennt, sondern man versucht auch nicht-konventionelle Wege zu gehen. Zu den konventionellen Prozessen gehören Techniken, die für den Durchbruch in der Mikroeletronikindustrie maßgebend waren: die Foto-, die Raster-Elektronenstrahl- oder die Raster-Ionenstrahl-Lithografie. Diese Techniken sind kommerziell erhältlich und in der Industrie weit verbreitet. Sie sind im Schnitt teuer und daher nur bedingt ertragreich. Ein großer Nachteil ist zusätzlich ihre Anwendbarkeit auf wenige, ausgewählte Materialien und Konfigurationen, wie Halbleiter oder planare Oberflächen. Diese Techniken setzen die Materialien korrosiven Ätzmitteln, hochenergetischer Strahlung, Vakuum oder hohen Temperaturen aus. Um empfindlichere Materialien wie Polymere verarbeiten zu können müssen „sanftere“ Prozesse entwickelt werden. Zu diesen nicht-konventionellen Prozessen gehören Techniken wie Mikrokontakt-Drucken (micro-contact printing), Selbstorganisation (self assembly) oder rasterkraftmikroskopbasierte Lithografie. Sie werden auf industrieller Ebene noch wenig genutzt und oft nur in der Forschung verfolgt. Sie bieten meist günstige Alternativen, sind aber häufig noch von der vollen Marktreife entfernt.
2. Mikro-Arrays mittels selektiver Substratquellung
Eine Polymeroberfläche wird durch eine Lochmaske aus Metall oder Kunststoff zuerst abgedeckt und anschließend entweder durch eine Goldschicht, durch Plasma oder durch UV-Strahlung mikrostrukturiert (Abb. 1a). Das Muster der Lochmaske wird so auf die Polymeroberfläche übertragen [1] und die oberste Schicht des Polymers wird dadurch entweder lokal abgedichtet oder vernetzt. Die Abdichtung besteht normalerweise aus einer 20 bis 50 nm dicken Goldschicht, während die vernetzte Schicht im Normalfall eine Dicke von 10 bis 20 nm besitzt [2]. Im darauf folgenden Schritt wird die mikrostrukturierte Oberfläche einem für das Polymer geeigneten Lösungsmittel oder dessen Dämpfen ausgesetzt. Das Lösungsmittel bewirkt eine lokale Quellung des Polymers, und zwar nur dort, wo es nicht abgedeckt oder vernetzt worden ist. Beispielsweise ist es mit dieser Methode möglich, mit Toluol als Lösungmittel großflächig bis zu 2,5 µm hohe Strukturen aus einer Polystyrolplatte „herauswachsen“ zu lassen (Abb. 1b). Der Boden der hieraus entstehenden Mikroküvetten besteht aus vernetztem Polymer, weil dort Plasma durch die Löcher der Maske an die Oberfläche gelangt ist.
Man kann die Methode aber auch anders einsetzen: Zuerst wird durch eine Lochmaske Gold auf die Oberfläche deponiert, dann wird die Maske entfernt und das Polymer wird mit Plasma behandelt. Diesmal werden die Flächen vernetzt, die nicht in Übereinstimmung mit den Löchern der Maske waren, die also nicht durch die Goldschicht geschützt wurden. Im Anschluss wird das Gold von der Oberfläche gelöst, das Polymer dem Lösungsmittel ausgesetzt und zum Quellen gebracht (Abb. 1c). Im Gegensatz zur ersten Technik, ragen hier am Ende des Prozesses die komplementären Flächen plastisch aus der Oberfläche heraus. Beide Anwendungsarten gewährleisten dieselbe laterale und vertikale Auflösung für die Bildung von Strukturen. In X- und Y-Richtung liegt sie knapp unter 5 µm und ist durch die Strukturgröße der Lochmaske gegeben, während sie in Z-Richtung unter 10 nm liegt und durch die Geschwindigkeit des Quellprozesses beeinflusst wird.
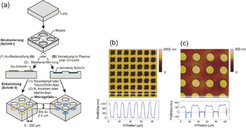
3. Nano-Arrays mittels Indentation mit Nanospitzen und anschließendes Quellen
Mit einer Abwandlung der oben präsentierten Technik ist es auch möglich, eine hohe laterale Auflösung zu erreichen. Dafür wird eine Polymeroberfläche durch Plasma oder UV-Strahlung großflächig vernetzt (Abb. 2a). Dadurch bildet sich eine dünne Schicht von vernetztem, hartem Polymer [2]. Darauf folgt eine Strukturierung der Oberfläche mittels Nanoindentation mit dem Rasterkraftmikroskop (AFM, atomic force microscope): Eine pyramidale AFM-Spitze wird nach einem zweidimensionalen, vorgegebenen Raster wiederholt auf die Oberfläche gedrückt. Dadurch erzeugt man Löcher, die tief genug sind, um die vernetzte Schicht zu durchbrechen. Danach setzt man das Polymer einem Lösungsmitteldampf aus, das Polymer quillt aus den Löchern heraus und bildet somit eine zweidimensionale Reliefstruktur aus „Nanokegeln“ (Abb. 2b) [3]. Parameter anhand dener der Prozess beeinflusst wird, sind die Dicke der vernetzten Polymerschicht, die Tiefe der Indentation mit der AFM-Spitze und die Quellzeit: Je länger die Probe dem Lösungsmittel ausgesetzt ist, desto höher und breiter werden die einzelnen Nanostrukturen (Abb. 2c).
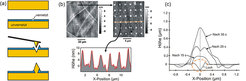
4. Mikrolinsen-Arrays mittels Inkjet-Technik und Lösungsmitteltropfen
Man kann mit Lösungsmittel Polymere auf verschiedene Art strukturieren. Durch das Auftragen eines kleinen Lösungsmitteltropfens (Volumen zwischen 0,1 und 1 nl) auf eine Polymeroberfläche ist es möglich, sphärisch geformte Mikrokrater herzustellen (Abb. 3a). Diese können in einem späteren Schritt mit einem zweiten Polymer ausgegossen und konvexe Mikrolinsen angefertigt werden. Das Lösungsmittel bewirkt drei unterschiedliche Effekte: (i) es löst das Polymer an, sodass der Tropfen nach einiger Zeit aus einer Polymerlösung besteht; (ii) es diffundiert in das Material hinein und bringt es zum Quellen; (iii) es weicht das Material auf, sodass es leicht deformierbar wird. Gleichzeitig verdunstet der Tropfen. Nach der vollständigen Verdunstung des Lösungsmittels bleibt ein konkaver Mikrokrater übrig [4]. Dieser entsteht durch eine Kombination chemischer und physikalischer Prozesse: (i) Der Tropfen, bestehend aus einer Lösungsmittel/Polymer-Mischung, verdunstet nicht gleichmäßig, sondern verstärkt am Rand (an der „Dreiphasenkontaktlinie“). Dadurch fließt die Mischung von der Mitte zum Rand des Tropfens, wo das Lösungsmittel verdunstet und das Polymer abgelagert wird; (ii) der Tropfen übt zweierlei Kräfte auf das aufgeweichte Polymer aus: die Oberflächenspannung zieht am Rande des Tropfens „nach oben“ und bewirkt die Bildung des externen „Rings“, der aus der Oberfläche herausragt; der tropfeninterne Druck (Laplace-Druck) drückt mit einer gleichmäßigen Kraft die gesamte vom Tropfen bedeckte Oberfläche „nach unten“ und bewirkt die Bildung der zentralen „Vertiefung“.

Eine einfache Technik zur Erzeugung kleinster Lösungsmittel-Volumina ist die so genannte Inkjet- oder Tintenstrahl-Technik [5]. Tropfendurchmesser zwischen 10 und 100 µm (die ungefähr Volumina zwischen 1 pl und 1 nl entsprechen) sind heutzutage Standard. Mit einem automatisierten, in X,Y und Z kontrollierten Tropfengenerator kann man zweidimensionale Arrays von Mikrokratern erzeugen (Abb. 3b). Durchmesser und Tiefe der Mikrokrater kann durch die Anzahl der Tropfen kontrolliert werden, wie in den Querschnitten (Abb. 3b unten) gezeigt wird: Entlang der X-Achse wurde die Anzahl der Tropfen konstant gehalten und somit auch die Tiefe der Krater; entlang der Y-Achse wurde die Anzahl der Tropfen erhöht und somit auch die Tiefe der modellierten Krater. Dieses Array wurde mit einem Elastomer (PDMS, Polydimethylsiloxan) ausgegossen, um plano-konvexe Mikrolinsen anzufertigen. Deren Brennweite wurde experimentell mit einem konfokalen Laser-Rastermikroskop gemessen (Abb. 3c). Die Linsen werden von der flachen Seite mit parallelem Laserlicht bestrahlt, das durch die Linsen gebündelt und fokussiert wird. Die Intensität des gebündelten Lichts ist im Fokus am höchsten, wie auch der Querschnitt der Intensität des transmittierten Lichts zeigt. Der Abstand zwischen dem Punkt höchster Intensität und der planaren Oberfläche gibt die Brennweite. Man kann die Brennweite auch aus geometrischen Parametern, wie etwa dem Brechungsindex des Materials und dem Krümmungsradius der Linse berechnen. Ein Vergleich der berechneten und der gemessenen Brennweiten zeigt eine sehr gute Übereinstimmung (Abb. 3d). Insgesamt besitzen die Mikrolinsen der mit dieser Technik hergestellten Arrays sehr gute optische Eigenschaften sowie eine Oberflächenrauhigkeit im Nanometerbereich.
Ausblick
Die Mikro- und Nanostrukturierung von Polymeroberflächen ist auch mit nicht-konventionellen Methoden möglich und durchaus erfolgreich. Alle drei präsentierten Techniken basieren auf sehr einfachen Mitteln. Es sind kein Vakuum, keine Hochenergiestrahlung und keine hohen Temperaturen notwendig. Der als erster beschriebene Prozess ist zur Parallelproduktion von Strukturen und damit von hohen Stückzahlen geeignet. Im Gegensatz dazu sind der zweite und dritte Prozess eher zur Erzeugung einzelner Mikrostrukturen (Anwendungen im Forschungs- und Entwicklungsbereich) gedacht. Alle drei Prozesse befinden sich zurzeit noch in einer prä-kommerziellen Entwicklungsphase, in der ihr Potenzial untersucht wird [6, 7].